The oldest in the industry research and project institute of oil refining and petrochemical industry of OJSC «VNIPIneft», which has its history since 1929, is today in its production potential, technical equipment, The volume of work performed and the scale of orders received by one of the leading Russian engineering companies in the field of oil and gas processing, petrochemistry, chemistry and development of oil fields. Throughout its existence, the Institute has continuously introduced new technologies and approaches in the field of design, as well as the adaptation of new software emerging in the market. The article is devoted to the experience of introduction and use in JSC «VNIPIPIneft» of software of AVEVA Engineering for improvement of automation design processes.
Since 2002 the Institute has successfully used PDMS technology to work with the 3D-model of the object (fig. 1). The created catalogue database contains almost all the elements that can meet when working on the project. To increase the productivity of specialists working with PDMS, JSC «VNIPIneft» is continuously developing both specialized macros and individual programs. To date, a unique set of proprietary programs has been created, which significantly expand standard functionality PDMS, significantly speed up the work process and improve the quality of released projects.
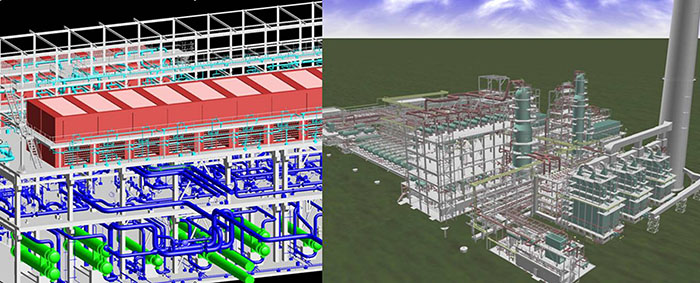
In addition to creating programs that expand the capabilities of PDMS, the institute is developing its own programs that cover all areas of the design process, including the development of highly specialized computational applications. Currently, the CAD system in JSC «VNIPIneft» is a complex hybrid structure (fig. 2), which is based on a set of production programs of AVEVA, such as PDMS, Diagrams, Instrumentation and Engineering. Complements this set of more than 100 other engineering, computing and office applications, programs for the preparation of drawings (AutoCAD with many different additions to it). The CAD system also interacts with the electronic document management system and the project document electronic archive system. The Institute uses a wide variety of in-house software interfaces to automate the exchange of data between a variety of specialized software, as well as between AVEVA family programs.
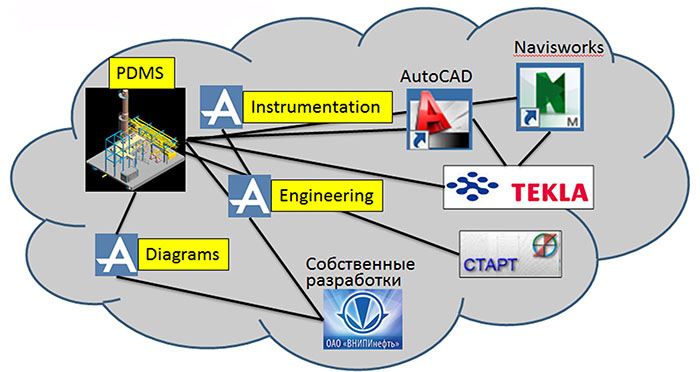
The ever-increasing number of project data circulating between departments, frequent customer changes, and the complex and not always transparent flow of data between production departments inevitably increase the likelihood of errors. To solve these and other problems, JSC «VNIPIneft» started the process of transition to design using the unified information model of the facility. This approach implies the creation of a single database of the project site in which all project information is stored, and this information is always up to date. The AVEVA Engineering application was selected as the main software tool for this approach.
The development of a proprietary software tool was also considered an alternative. Despite the fact that the Institute has enough resources and qualified programmers to create programs of this level, it was decided in favor of the finished product available on the market. One of the reasons for this decision was that all software tools require continuous additions and improvements, otherwise they will very soon no longer meet the requirements of users, and these requirements are known to change constantly. Therefore, in the long term, which is more than 5 years, the cost of supporting and developing your own program will be very significant and comparable to the cost of buying a ready-made solution.
Like any new program that appears on the market, the Engineering application in the current version so-It also has the potential to improve its functionalities and is not fully adapted to the task of creating a single information model at the institute. Therefore, the positive impact of the programme is not expected until 2016.
Why did the institute start to implement this program now, rather than wait for a new version? The practice of many companies shows that when implementing any program there is always a large number of employees of production departments, which (for various reasons) have internal resistance and reluctance to use new programs. This inertia can be overcome, but it must be done gradually, otherwise there can be very strong opposition that can significantly slow down or stop the process of introducing new technology. Employees of production departments need to be slowly drawn into new processes, day by day recalling the goal to which the company is going. The critical number of staff who have mastered the new programme and adopted new approaches is reaching a turning point within the team, and the rest of the staff inevitably moves to the new programme. It is for these reasons that the Institute proceeds, introducing the Engineering application in the form in which it is now, clearly setting the course in which the company is moving in terms of automation.
Objectives of AVEVA Engineering Implementation
The implementation process started at the end of 2014. We list the main objectives of the implementation.
1st objective: streamline engineering information flows. The design process necessarily involves the interaction of production departments, both among themselves and with other organizations involved in the project, as well as with the customer. The chaotic and opaque nature of the information flow system may cause the necessary information not to reach all interested persons in the production departments or they receive it with considerable delay in time, which in turn increases the likelihood of project errors and leads to a longer design time. Our goal is to create a more transparent, simple and understandable notification system for changes in project data.
2nd objective: to synchronize the information stored in different programs, which are staffed by employees of different departments. The problem here is that, for one reason or another, information about the same design object (for example, equipment) may differ from one production department to another at the same time. This may result in the issuance of documentation containing outdated data, requiring subsequent changes and longer design times. The data synchronization system is designed to detect outdated information in the project, thereby improving the quality of the project.
3d objective: to reduce the probability of errors in the output documentation. The reasons for errors in the output documentation are many, but there is a direct relationship between the frequency of changes in the source data by the customer and the probability of occurrence of an error. Most errors are made due to lack of attention when processing large amounts of information in a short time. After all, even a small mistake made in one department and passed as a task to another, can cause a chain reaction with the appearance of a mass of errors at once. Therefore, the creation of a data synchronization system based on the Engineering application will create an additional tool to check the correctness of the information, which will positively affect the quality of the output documentation.
4th objective: to accelerate project release by optimizing design processes. The process of introduction of the Engineering application inevitably leads to revision of existing design processes in the Institute. The Engineering approach to design is becoming more object-oriented as opposed to the existing documentation-oriented approach. You can apply parallel design elements. Delays are eliminated when raw data provided by the requisitioner is incomplete. By creating a central repository of information in the form of a Engineering database, many intermediate elements will be reduced in the design process. For example, there will be no need to exchange documents between departments to perform the reconciliation, because all information on the project is in one database and is available to all project participants.
5th objective: Automate the transfer of tasks between departments. To solve this interesting problem can be many different ways, and each company chooses the one that best suits it due to the circumstances. In JSC «VNIPIneft» this task is solved using Engineering application, which makes it possible to review the way in which tasks are currently routinely transferred from division to division in the form of a set of documents in electronic or paper format and to move to related divisions by changing the status of readiness of the element in a single database.
6th: to accelerate the search for information in the project. Practice shows that employees of production departments spend a significant part of their time searching for the necessary information. If a single data warehouse is used, all project participants can quickly search for information and be confident that the information found is up to date at the time of search. In addition, the use of distributed attributes allows you to see a complete set of item data filled in by different departments separately.
7th: to improve project manageability. By applying the element status system to the data stored in the Engineering database, project managers are able to continuously monitor the current status of the project and receive various types of reports for timely decision-making.
Fig.3 Fig.4
Fig. 3 presents a simplified scheme of information flows between various AVEVA modules and other engineering programs that are used in JSC «VNIPIneft». As can be seen from the chart, information flows to organizations are a very confusing picture, with only the main elements of a real system identified.
Fig. 4 shows a diagram of information flows using the Engineering application. It is worth noting at once that it cannot solve all the problems related to data synchronization, but its use allows to some extent to streamline the numerous information flows that exist when working on the project. Engineering acts as a dispatcher that manages information circulating between engineering applications and allows you to put more order into the system.
Fig.5 Fig.6
Fig. 5 shows the flow chart of the output documentation. The information in the documents comes from different programs used in different departments. In such an approach, under certain circumstances, it is likely to be a problem of mis-chronization of data and outdated information in the output.
When using the Engineering application (fig. 6), documents are formed from a single database, the information in which is always in the current state, which eliminates the possibility of getting outdated information in the output document. It also greatly simplifies the process of creating revisions, as documents are linked to only one database, in which the history of changes is directly stored.
The main stages of AVEVA Engineering implementation
In the first phase, an implementation team was formed. Since the Engineering application affects all major production departments, representatives of the following departments were included in the implementation team: technological, installation, control and measurement department and electrical engineering. Particular attention should be paid to the correct selection of the members of the implementation team, as the results of their work will determine the success of further implementation of the programme.
After the formation of the implementation team, their external training was conducted at the AVEVA office. Also, the training course was attended by specialists of the IT department involved in the administration of the Engineering application. Further, in accordance with the implementation plan, a pilot project was carried out to test all possibilities of the software product and to work out the main interdivisional scenarios that most often arise during the actual project. For the pilot project, a simplified model of the real object was chosen, including the whole set of unique elements. The implementation of the pilot project on a simplified model allowed to reduce the time without loss of quality.
The pilot project showed that the Engineering functionality mostly allows to realize the goals of the institute. At the same time, certain parts of the program require adaptation to the specifics of the company. This kind of adaptation involves creating your own addins in C#. As a result, the institute will use a system consisting of a Engineering application as the basis and set of its own extensions. Basically the extension of the application functionality will affect the synchronization system and notification system.
It is important to understand that the introduction of Engineering leads to significant changes in the design processes. Therefore, at the same time as the pilot project in JSC «VNIPIneft» internal audit of the design processes in production departments was carried out, as well as checking of the level of automation and the step-neither use of PDMS. Based on the results of the audit, a plan was formed to review the approaches available at the Institute and to develop new maps of the interaction of departments taking into account the use of Engineering. These tasks are time consuming, but it is clear that without clearly defined regulations and interaction schemes, the implementation of Engineering is doomed to failure. At present, the Institute is developing a system of automatic synchronization of data between different programs, by means of which data that have reached a certain status will be automatically synchronized with the Engineering database (fig. 7).
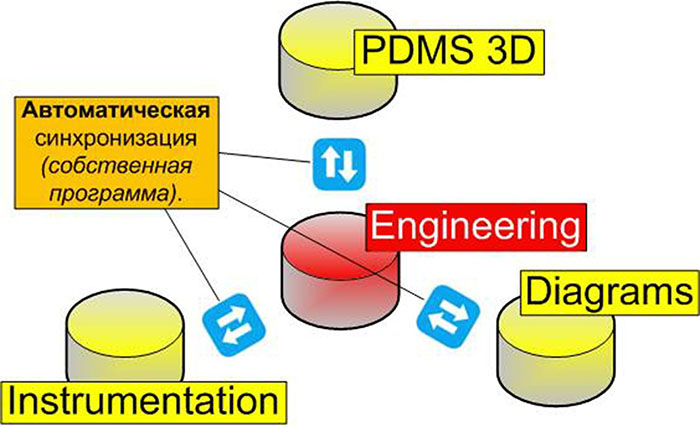
The main difficulties in the implementation of the Engineering application arise at the beginning because the company’s employees need to get used to new ways of work. Therefore, in the first stages it is necessary to attract the most loyal and involved employees. After a critical mass of people has mastered the technology, the implementation process will go by inertia. The selection of members of the implementation team should be carried out by the specialist responsible for the implementation of the program. It is important to take into account the presence of team members not only good qualifications in their subject area at the same time a high level of computer literacy, but also their personal qualities. After all, the speed and quality of implementation depend on the work of the team. These officers will then become centres for the dissemination of new ideas in their production departments.
Since it is not possible to take into account all the details and nuances of the real project at the first stages of implementation, implementation is carried out in several iterations, each of which covers the entire chain of information flow between departments. Each subsequent iteration is filled with more detail and takes into account more specific cases encountered in real projects. This approach, on the one hand, increases the time of implementation of the program, but on the other, reduces the risks associated with the implementation of the program on a real project. As there are no two identical companies, there is no single approach to software implementation. Each company has its own unique features and developed years of practice. We hope that the experience of introduction of AVEVA Engineering technology in JSC «VNIPIneft» with rich possibilities for integrated design, It will be useful to colleagues in the workshop and will help them to find their way to organize an effective information exchange between project teams.
Date of publication: 20 May 2015
Source: isicad.ru
The oldest in the industry research and project institute of oil refining and petrochemical industry of OJSC «VNIPIneft», which has its history since 1929, is today in its production potential, technical equipment, The volume of work performed and the scale of orders received by one of the leading Russian engineering companies in the field of oil and gas processing, petrochemistry, chemistry and development of oil fields. Throughout its existence, the Institute has continuously introduced new technologies and approaches in the field of design, as well as the adaptation of new software emerging in the market. The article is devoted to the experience of introduction and use in JSC «VNIPIPIneft» of software of AVEVA Engineering for improvement of automation design processes.
Since 2002, the Institute has successfully used PDMS technology to work with a 3D model of an object (Fig. 1). The created catalog database contains almost all the elements that can be encountered when working on a project. In order to increase the productivity of specialists working with PDMS, VNIPIneft OJSC is continuously developing both specialized macros and individual programs. To date, a unique set of self-developed programs has been created that significantly expand the standard functionality of PDMS, significantly speed up the workflow and improve the quality of the projects produced. PDMS, значительно ускоряют рабочий процесс и повышают качество выпускаемых проектов.
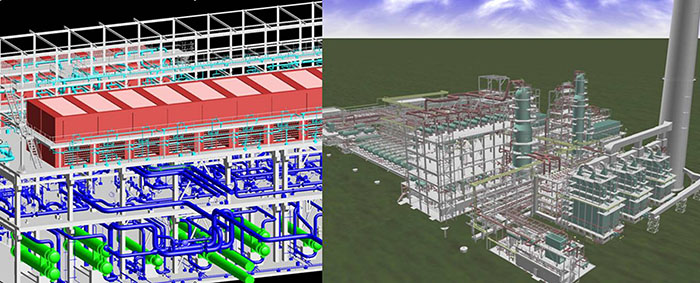
In addition to creating programs that expand the capabilities of PDMS, the institute is developing its own programs that cover all areas of the design process, including the development of highly specialized computational applications. Currently, the CAD system in JSC «VNIPIneft» is a complex hybrid structure (fig. 2), which is based on a set of production programs of AVEVA, such as PDMS, Diagrams, Instrumentation and Engineering. Complements this set of more than 100 other engineering, computing and office applications, programs for the preparation of drawings (AutoCAD with many different additions to it). The CAD system also interacts with the electronic document management system and the project document electronic archive system. The Institute uses a wide variety of in-house software interfaces to automate the exchange of data between a variety of specialized software, as well as between AVEVA family programs.
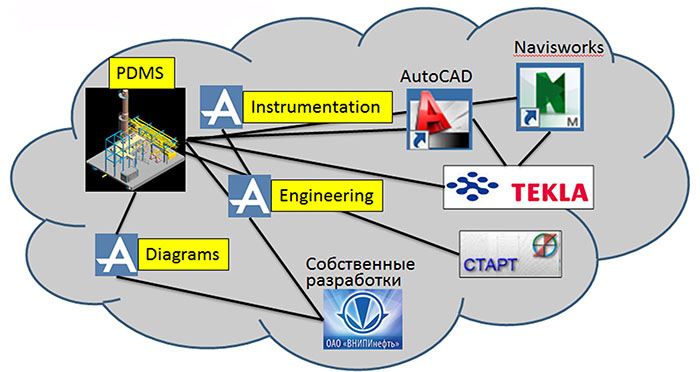
The ever-increasing number of project data circulating between departments, frequent customer changes, and the complex and not always transparent flow of data between production departments inevitably increase the likelihood of errors. To solve these and other problems, JSC «VNIPIneft» started the process of transition to design using the unified information model of the facility. This approach implies the creation of a single database of the project site in which all project information is stored, and this information is always up to date. The AVEVA Engineering application was selected as the main software tool for this approach.
Since 2002, the Institute has successfully used PDMS technology to work with a 3D model of an object (Fig. 1). The created catalog database contains almost all the elements that can be encountered when working on a project. In order to increase the productivity of specialists working with PDMS, VNIPIneft OJSC is continuously developing both specialized macros and individual programs. To date, a unique set of self-developed programs has been created that significantly expand the standard functionality of PDMS, significantly speed up the workflow and improve the quality of the projects produced.
Like any new program that appears on the market, the Engineering application in the current version also has quite a lot of potential in terms of improving its set of functionality and is not fully adapted to solve the problem of creating a unified information model at the institute. Therefore, the appearance of a positive effect from the implementation of this program is expected no earlier than 2016.
Why did the institute start implementing this program now, and not wait for a newer version? As the practice of many companies shows, when implementing any program, there is always a large number of employees of production departments who (for various reasons) have internal resistance and unwillingness to use new programs. This inertia can be overcome, but it must be done gradually, otherwise you may encounter very strong opposition, which can significantly slow down or even stop the process of introducing a new technology. Employees of production departments need to be slowly drawn into new processes, day after day reminding them of the goal the company is moving towards. Upon reaching a critical number of employees who have mastered the new program and adopted new approaches, a turning point occurs within the team, and the rest of the employees inevitably switch to using the new program. It is from these considerations that the institute proceeds, introducing the Engineering application in the form in which it is now, unambiguously setting the course in which the company is moving in terms of automation.
Objectives of AVEVA Engineering Implementation
The application implementation process began at the end of 2014. Let's list the main implementation goals.
1st goal: to streamline the flow of engineering information. The design process is inevitably associated with the interaction of production departments both among themselves and with other organizations involved in the project, as well as with the customer. The randomness and opacity of the information flow system can lead to the fact that the necessary information is not received by all interested persons in production departments or they receive it with a significant time delay, which in turn increases the likelihood of errors in the project and leads to an increase in design time. Our goal is to create a more transparent, simple and understandable system of notifications about changes in project data.
2nd goal: to synchronize information stored in various programs in which employees of different departments work. The problem here is that for one reason or another, the information on the same design object (for example, equipment) in different production departments at the same time may differ. This may lead to the release of documentation containing outdated data, which entails the need for subsequent changes and an increase in design time. The data synchronization system is created to detect the presence of outdated information in the project, thereby increasing the quality level of the project being performed.
3rd goal: to reduce the likelihood of errors in the output documentation. There are a lot of reasons for errors in the output documentation, but there is a direct relationship between the frequency of changes in the source data by the customer and the probability of an error. Most mistakes are made due to inattention when processing a large amount of information in a short time. After all, even a small mistake made in one department and transferred as a task to another can cause a chain reaction with the appearance of a mass of errors at once. Therefore, the creation of a data synchronization system based on the Engineering application will create an additional tool for verifying the correctness of information, which will positively affect the quality of output documentation.
4th goal: accelerate the release of projects by optimizing design processes. The process of implementing the Engineering application inevitably leads to a revision of the existing design processes at the Institute. The Engineering approach to design is becoming more object-oriented as opposed to the existing document-oriented approach. It becomes possible to apply elements of parallel design. Delays in work are eliminated in cases when the initial data provided by the customer is incomplete. By creating a central repository of information in the form of an Engineering database, many intermediate elements will be reduced in the design processes. For example, there will be no need to exchange documents between departments to perform coordination, because all information on the project is in one database and is available to all project participants.
5th goal: to automate the transfer of tasks between departments. There are many different ways to solve this interesting problem, and each company chooses the one that suits it best due to the circumstances. At VNIPIneft, this task is solved using the Engineering application, which allows you to revise the currently familiar method of transferring tasks from department to department in the form of a set of documents in electronic or paper format and make the transition to issuing tasks to related departments by changing the readiness status of an element in a single database.
6th goal: to speed up the search for information in the project. Practice shows that employees of production departments spend a significant part of their working time searching for the necessary information. In the case of using a single data warehouse, all project participants can quickly search for information and be sure that the information found is relevant at the time of the search. In addition, the use of distributed attributes allows you to see the full set of data on the element, filled in by different departments separately.
7th goal: to improve the manageability of the project. By applying the item status system to the data stored in the Engineering database, project managers are able to constantly monitor the current status of the project and receive all kinds of reports to make timely decisions.
-
Fig.3 -
Fig.4
Fig. 3 presents a simplified scheme of information flows between various AVEVA modules and other engineering programs that are used in JSC «VNIPIneft». As can be seen from the chart, information flows to organizations are a very confusing picture, with only the main elements of a real system identified.
Figure 4 shows a diagram of information flows using the Engineering application. I would like to note right away that it is impossible to solve all the problems associated with data synchronization with its help, but its use allows you to sort out to some extent the numerous information flows that exist when working on a project. Engineering acts as a dispatcher that manages the information circulating between engineering applications and allows you to bring more order to the system.
-
Fig.5 -
Fig.6
Figure 5 shows a scheme for obtaining output documentation. The information in the documents comes from various programs used in different departments. With this approach, under certain circumstances, there is a possibility of encountering the problem of data desynchronization and outdated information getting into the output documentation.
When using the Engineering application (Fig. 6), documents are generated from a single database, the information in which is always up to date, which eliminates the possibility of outdated information entering the output document. The process of creating revisions is also greatly simplified, since the documents are associated with only one database, in which the history of changes is directly stored.
The main stages of AVEVA Engineering implementation
At the first stage, an implementation team was formed. Since the Engineering application affects all the main production departments, representatives of the following departments were included in the implementation team: technological, installation, control and measuring devices and electrical engineering. Special attention should be paid to the correct selection of the implementation team members, since the success of further implementation of the program will depend on the results of their work.
After the formation of the implementation team, their external training was conducted at the AVEVA office. Also, the training course was attended by specialists of the IT department involved in the administration of the Engineering application. Further, in accordance with the implementation plan, a pilot project was carried out to test all possibilities of the software product and to work out the main interdivisional scenarios that most often arise during the actual project. For the pilot project, a simplified model of the real object was chosen, including the whole set of unique elements. The implementation of the pilot project on a simplified model allowed to reduce the time without loss of quality.
The pilot project showed that the Engineering functionality for the most part makes it possible to realize the goals facing the institute. At the same time, certain parts of the program require adaptation to the specifics of the company. This kind of adaptation involves creating your own addins in C#. As a result, the institute will use a system consisting of an Engineering application as a basis and a set of its own extensions. Basically, the extension of the functionality of the application will affect the synchronization system and the notification system.
It is important to understand that the introduction of Engineering leads to a significant change in the design processes. Therefore, simultaneously with the pilot project, VNIPIneft carried out an internal audit of the design processes in the production departments, as well as checking the level of automation and the degree of use of PDMS. Based on the results of the audit, a plan was formed to revise the approaches available at the Institute and draw up new maps of interaction between departments, taking into account the use of Engineering. These works require considerable time, but it is quite obvious that without drawing up clearly prescribed regulations and interaction schemes, the implementation of the Engineering application is doomed to failure. Currently, the Institute is creating a system of automatic data synchronization between various programs, with the help of which data that has reached a certain status will be automatically synchronized with the Engineering database (Fig. 7).
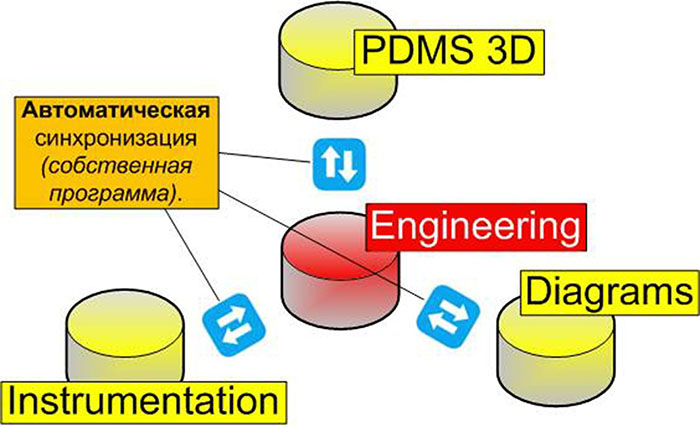
The main difficulties in implementing the Engineering application arise at the very beginning due to the fact that the company's employees need to get used to new ways of working. Therefore, at the first stages it is necessary to attract the most loyal and involved employees. After a critical mass of people who have mastered the technology has accumulated, the implementation process will already go by inertia. The specialist responsible for the implementation of the program should be engaged in the selection of members of the implementation team. It is important to take into account that the team members have not only good qualifications in their subject area at the same time with a high level of computer literacy, but also their personal qualities. After all, the speed and quality level of implementation directly depends on the work of the team. Subsequently, these employees will become centers for the dissemination of new ideas in their production departments.
Since it is impossible to take into account all the details and nuances of a real project at the first stages of implementation, the implementation is carried out in several iterations, each of which covers the entire chain of information movement between departments. Each subsequent iteration is filled with more detailed details and takes into account more special cases encountered in real projects. With this approach, on the one hand, the implementation time of the program increases, but on the other hand, the risks associated with the implementation of the program on a real project decrease. As there are no two identical companies, so there is no single approach to the implementation of software tools. Each company has its own unique features and practices developed over the years. We hope that the experience of implementing AVEVA Engineering technology in VNIPIneft, which has rich opportunities for integrated design, will be useful to colleagues in the workshop and will help them find their way to organize effective information exchange between project teams.
Date of publication: 20 May 2015
Source: isicad.ru